ここでは、製品開発にシミュレーション(CAE)がどのような役割を果たしているのか、シミュレーションのメリットについて、自動車の製品開発を例にして説明します。
シミュレーション(CAE)に期待される役割
シミュレーション(CAE)に期待される役割には、次のようなものがあります。
- 開発期間短縮
- 新製品の早期市場投入
- 試作・実験コストの削減
次に、シミュレーションが試作や実験よりも優れているポイントを列挙してみます。
- 試作が困難な製品開発への対応
- 高い精度が要求される製品設計
- 厳しい安全性要求への対応
- 試験条件(例えば境界条件、固定、自由、ばね支持など)による比較が簡単
- シミュレーションでは、条件設定を変更するだけで結果を得られます。
- 実験では試験条件をそろえるのも一苦労です。
- 実験での再現が難しい条件設定
- 計測の難しい現象の確認
- ねじりの振動モード形状など
また、シミュレーションでなければできないこともあります。
- 計測できない場所の応力値などを知りたい。
- 水中や真空中など特殊な環境での実験
シミュレーション(CAE)の使われ方と注意点
解析専任者と、解析専任ではない人とでは、シミュレーションを使う目的・用途が下表の様に異なります。
|
解析専任者 |
解析専任ではない人 |
---|---|---|
CAEへの要求 |
|
|
解析内容 |
|
|
ツール |
|
|
このため解析目的により実際にやることが違ってくるため、シミュレーションを始める前に、「何のために解析するのか」を明らかに、できるだけ具体的にイメージすることがポイントになります。
解析目的の例としては、
- 実験データと合わせこみたい。
- 設計案の比較をして、傾向をつかみたい。
- 実験で検証できない現象を調べたい。
といったことがあり、各々の要求に対し条件設定や解析精度などが違ってきます。
製品開発のトータルコストを下げる取り組み
製品開発のトータルコストを下げるためにも、開発期間の短縮と試作レスへの挑戦は続いています。
製品開発のトータルコストを下げるためには、
- 製品開発前段でのシミュレーションの割合を増やす。
- 製品開発全体に占めるシミュレーションの割合を増やす。
これを並行して進める必要があります。下図はこのイメージ図です。
現在は、開発が進むにつれ、
- 実験(試験)のリソース(コスト)増加
- トータルの開発リソース増加
将来的には、以下の様にしていくイメージです。
- 開発初期のシミュレーションのリソースを増加
- 開発のトータルコストを削減
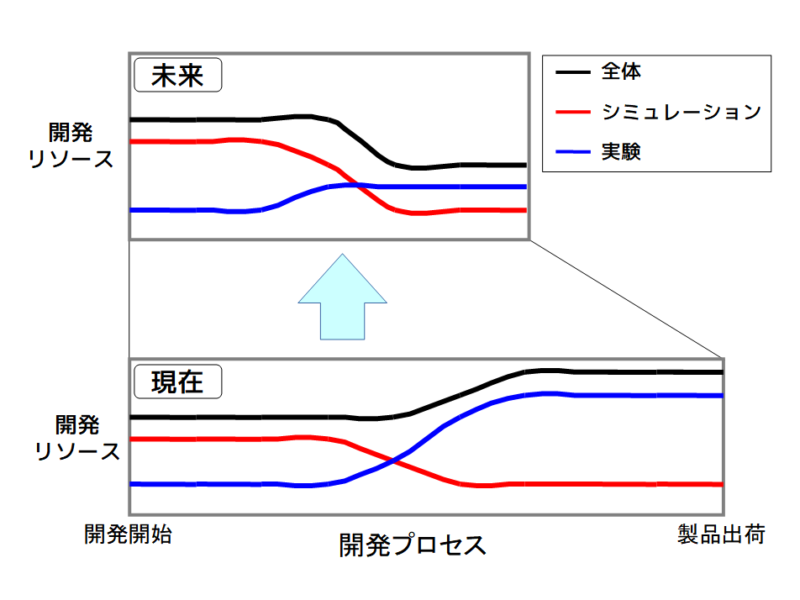
シミュレーションによる設計開発リソース削減イメージ
シミュレーション(CAE)の必要性:自動車の研究開発への要求
なぜシミュレーション(CAE)が必要なのでしょうか?
ここでは、自動車に求められる要求について考えてみます。
- 振動・騒音に関する要求
- 性能(燃費)と快適性
- 軽量化と高剛性
- ニーズの多様化
- 街乗り、長距離、輸送
- 環境
- リサイクル
- 省エネ、ハイブリッド
- 自動運転、予防安全(運転補助)
さらに、これらの要求全てをバランスよく満たすためには、
- 多目的な最適化
- 軽量化、衝突安全、居住性、デザイン、騒音・振動、環境対策等、様々な要求をバランスよく満足させること
が必要となってきていますが、簡単なことではありません。
例えば、
燃費を良くするには軽量化が効果的ですが、
振動対策の面からは剛性が高い方がよい、
でも材料コストが上がるのは困る。
といったイメージになります。
製品開発の流れ:自動車を例に
自動車を例にざっくりと製品開発の流れについて説明します。
開発車のコンセプト
どのようなコンセプトの商品(車)とするのかを決めます。
例えば、
- 車のサイズは?
- ファミリー向け?
- 運転を楽しむスポーツタイプ?
などなど。
この段階で車の性能(例えば燃費や運動性能など)をシミュレーションできるとよいのですが・・・。
この段階では、
- 設計詳細は決まっていない。
- つまり、図面(=3Dの形状データ)がない。
- シミュレーションできない。
といった状態なので、形状モデル(3D CADのデータ)を使うシミュレーションツールは使えません。
粗い形状でシミュレーションすると結果の精度が低すぎてやはり使えないといったイメージになるかと思います。
設計(構想設計~詳細設計)
3D CADで形状ができあがってきます。
ボディや外装は結構変更が多いそうですが、フレームやエンジンなどは、小規模な変更にとどまることが多いそうです。
シミュレーションによる設計の最適化
シミュレーションによる様々な検証が行われ、試作品(実機)の詳細設計が進みます。
テスト(実験)による設計の最適化
実験や試験により、試作品候補を絞り込みます。
試作完了
シミュレーションやテスト結果により必要に応じ設計まで戻り、最終的に試作が完了すると、量産に移ります。
量産
量産試作、小ロット生産から始め、生産台数の増減などによる調整が行われます。
自動車の騒音・振動:NVH(騒音、振動、快適性)
自動車の騒音・振動は、車外と車内の騒音・振動とに分けられます。
例えば、以下のような騒音や振動が、社内に伝わり、騒音として運転者や同乗者に伝わります。
騒音の例
エンジン騒音、駆動系、車体の振動音、風切り音、タイヤ騒音、排気騒音
自動車のNVHとは、車両の振動、騒音及び乗り心地のことです。
- ノイズ(Noise)
- 車室内の騒音
- バイブレーション(Vibration)
- 主にエンジン及びタイヤから伝わってくるステアリングやシート、フロアの振動
- ハーシュネス(Harshness)
- 路面からの外乱により、ステアリングやシート、フロアに感じる振動
自動車の騒音・振動対策
自動車の場合も音から問題がみつかり、原因究明となることが多いようです。現象を確認しその原因を究明し、シミュレーションや実験で確認します。
対策は、まずは応急処置、その後恒久対策をとることが一般的です。例えば、応急処置では吸音材を貼り付け、恒久対策では設計変更をして吸音材を不要にするといったイメージです。
振動と騒音の発生から対策までの流れは、以下のようになります。
発見された問題:騒音が発生している
- 騒音(源)の特定
- 振動解析
- 対策(対策部品の付加や製品の設計変更など)
ここまでで対策完了とする場合が多いのではないかと思います。
ここから先は、騒音と振動の関係(相関)の話が出てくるのでなかなか難しいからです。
例えば、自動車のある部分を手で軽く抑えると(手が減衰材の働きをして)、振動が収まりきになっていた音も消えたとします。
これをシミュレーションで確認しようとすると、まず、振動と騒音の関係(相関)をどのように考えるかで悩むことになります。
部品間の振動の伝達については寄与率などを使い、どのような経路からどの程度の振動が伝わるかを表現します。
部品から出る音(放射音)についても同様に、どの部分(部品)が、問題となっている騒音に寄与しているかを求めることになります。
振動や騒音の寄与率は実測値を使い決めていくことになりますが、これはこれでシミュレーションの一分野になるほどの奥深さがあります。
まとめ
ここでは、製品開発にシミュレーション(CAE)がどのような役割を果たしているのか、シミュレーションのメリットについて、自動車の製品開発を例に以下の項目について説明しました。
- シミュレーション(CAE)に期待される役割
- シミュレーション(CAE)の使われ方と注意点
- 製品開発のトータルコストを下げる取り組み
- シミュレーション(CAE)の必要性:自動車の研究開発への要求
- 製品開発の流れ:自動車を例に
- 自動車の騒音・振動:NVH(騒音、振動、快適性)
- 自動車の騒音・振動対策